Making stretchers for oversized paintings
Conservation Frames and Furniture Studio
By Alex Forrest
Artlines | 3-2020 | September 2020
Two of the Gallery’s largest and most treasured paintings require special attention from conservators to stay in the best possible condition. Here, Alex Forrest elaborates on the technical elements of the preparation and maintenance of these generously proportioned works.
At approximately two metres high and six metres wide, Mirdidingkingathi Juwarnda Sally Gabori’s Dibirdibi Country 2008 and the collectively painted Makarrki – King Alfred’s Country 2008, led by Birmuyingathi Maali Netta Loogatha, are two of the largest works on canvas in QAGOMA’s Collection. These significant paintings by the Kaiadilt artists are frequently requested for loan by national and international art museums, and due to their size, they usually travel unstretched — removed from their timber support and rolled for safe transportation. The QAGOMA Conservation Frames and Furniture Studio (CFFS) undertook the in-house manufacture of new stretchers, and this article documents the challenges, processes and results of this project.
Both works are painted on commercially primed linen canvases. Before painting, the canvas (known as the primary support) is laid across the stretcher (the auxiliary support) and held in tension with staples. Unlike a strainer, which has fixed corners and is not adjustable, a stretcher relies on a tight-fitting, expandable corner joinery called a full-mitred bridle joint. Timber wedges or ‘keys’ are inserted into the interior corners of the joint, enabling the joint to expand and apply the necessary tension to the canvas. Expandable stretchers have been used for paintings on canvas since the mid-eighteenth century. For the best long-term condition of a painting, stretchers are preferred to strainers and are recommended to artists.
Large paintings such as these present design and construction challenges. They require adequate cross-bracing (a wooden framework) between the stretcher bars to increase its overall rigidity, and to allow good canvas tension without distorting the stretcher bars. Additionally, all horizontal stretcher bar and bracing components must have an integrated joint in the centre, enabling the stretcher to be disassembled into two halves for transport. We investigated various joinery methods, including traditional Japanese joinery, but in this instance we resolved to use an aluminium angle solution, incorporating a mortise and tenon joint (which connects two pieces together end to end) for increased strength and to help with alignment during the stretchers’ assembly. The aluminium angle is recessed into the stretcher bar, so that the canvas wrapped around it can remain flush. The aluminium is attached to the stretcher bar using countersunk bolts into heavy-duty insert nuts, suitable for repeated use.
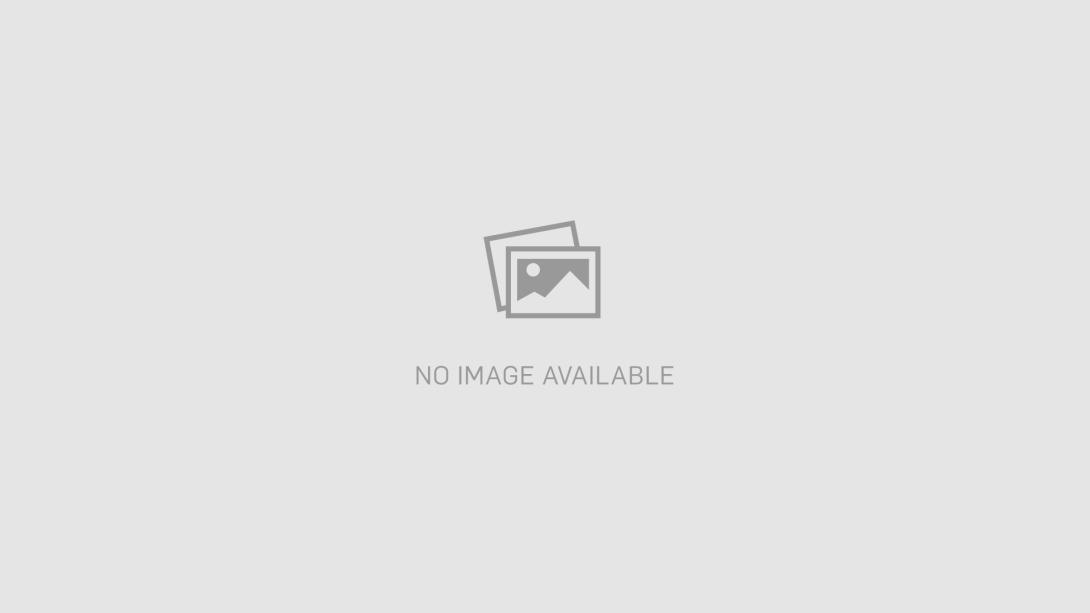
Stretchers under construction in the Conservation Frames and Furniture Studio, 2019 / Photograph: QAGOMA Conservation
Equipped with the machinery and expertise to manufacture the exacting products required, the CFFS’s first task is to select suitable lengths of rough-sawn timber boards. The boards are cut down to size using a panel saw, then the four sides of the timber are planed to the correct dimension in a process called jointing and thicknessing. The final step is undertaken with a Marunaka fixed-knife finish planer — a machine that works by pulling the timber past a stationary planer blade, taking an ultra-fine shaving from the face of the timber and eliminating the need for sanding.
Using the Stegherr BRF milling machine, our full-mitred bridle joints can be machined in one safe and efficient operation. This represents significant labour and cost savings in the fabrication of this complex joinery. It also facilitates later modification: if a stretcher bar is slightly too long in its final fitting, it can be shortened and re-machined to the millimetre. Having control over the entire manufacturing process ensures that the design of the stretcher can meet the exact needs of the artwork.
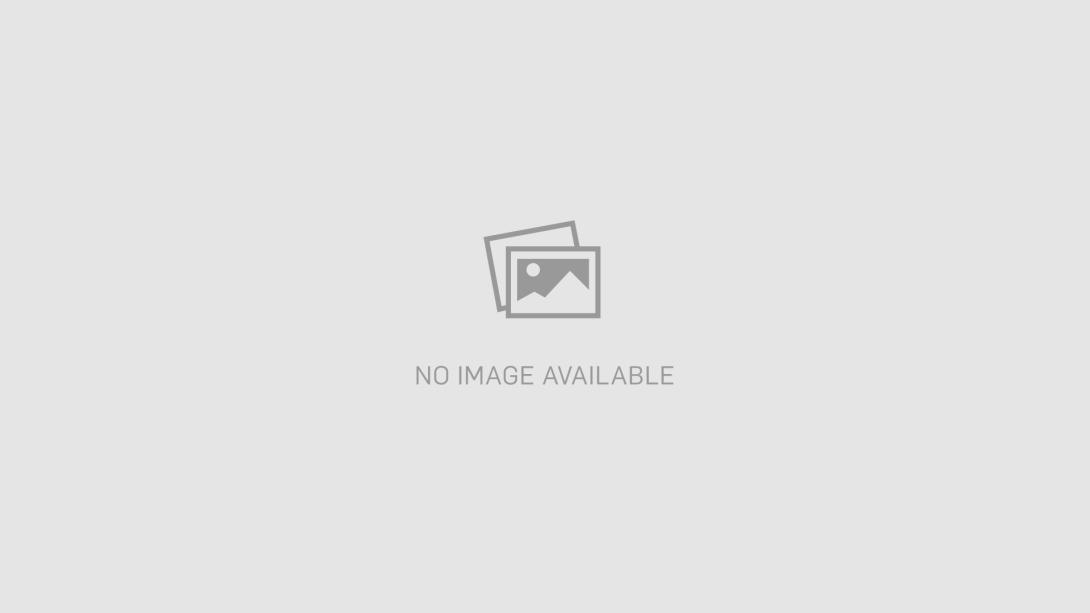
Stretchers under construction in the Conservation Frames and Furniture Studio, 2019 / Photograph: QAGOMA Conservation
Western Red Cedar (Thuja plicata), the timber used in the construction of the stretcher bars and cross-bracing, is a softwood that is lightweight, straight-grained, and has high dimensional stability, meaning it is unlikely to bow or twist. The keys are made from European Beech (Fagus sylvatica), a hardwood exhibiting high wear-resistance, hardness and strength. Special attention is paid to the grain direction of the keys during machining, as this is critical to the performance and longevity of the key. On completion of the stretcher bars, cross-bracing and keys, all the components are sealed with blonde de-waxed shellac to protect both the timber and the canvas.
The stretcher is then fully assembled and the hanging system is fitted: in the case of these two works, a plywood split batten is the preferred option for distributing the weight of the stretcher evenly across its length. A split batten consists of two interlocking profiles, mounted correspondingly to the back of the artwork and to the gallery wall. With the stretcher complete, the work is ready to hand over to the QAGOMA painting conservators, who undertake the careful process of stretching the artwork.
Alex Forrest is Conservation Workshop Technician.

Makarrki - King Alfred's Country 2008
- LOOGATHA, Birmuyingathi Maali Netta - Artist
- GABORI, Mirdidingkingathi Juwarnda Sally - Artist
- THOMAS, Warthadangathi Bijarrba Ethel - Artist
- MOODOONUTHI, Thunduyingathi Bijarrb May - Artist
- PAUL, Kuruwarriyingathi Bijarrb Paula - Artist
- NARANATJIL, Wirrngajingathi Bijarrb Kurdalalngk Dawn - Artist
- LOOGATHA, Rayarriwarrtharrbayingathi Mingungurra Amy - Artist